Why Carbon for MedTech?
Carbon’s full suite of hardware, software, and materials are engineered to work together to create breakthrough products that can be produced in orders of hundreds to hundreds of millions.
Design Freedom
- Mass customization
- Lattices & digital texturing
- Complex unmoldable features
Engineering Materials
- Engineering-grade, end-use materials
- Wide variety of rigid and elastomeric materials
- Biocompatible-capable and sterilizable materials
Faster Path to Market
- Rapid design iterations
- No tooling costs
- Carbon Production Network Partners with ISO certifications
Traceable Process
- 100% digital workflow
- Analyze operational metrics
- Print identifiers directly on parts
Mass Customization Heroes
mign, a digital orthopedics company, produces personalized orthopedic products at scale with the Carbon platform to meet the unique needs of each patient they treat.
The Path to Production With Carbon
Carbon’s advanced additive manufacturing technology transforms the MedTech design and production process, offering faster, patient-specific solutions with consistent accuracy and repeatability.
Phase 1: Discovery + Design
During discovery, Carbon can assess and optimize your design files for printability or connect you with one of our ISO 13485-certified production partners to get started right away. We can support your product development cycle by working on design iterations and prototypes for validation.
Phase 2: Path to Production
In the production phase, we align on goals including cost and timeline. From there, you can get into production with a member of our CPN network, which includes experts in ramping applications to production with the Carbon platform, or we can help you validate your own printer for production.
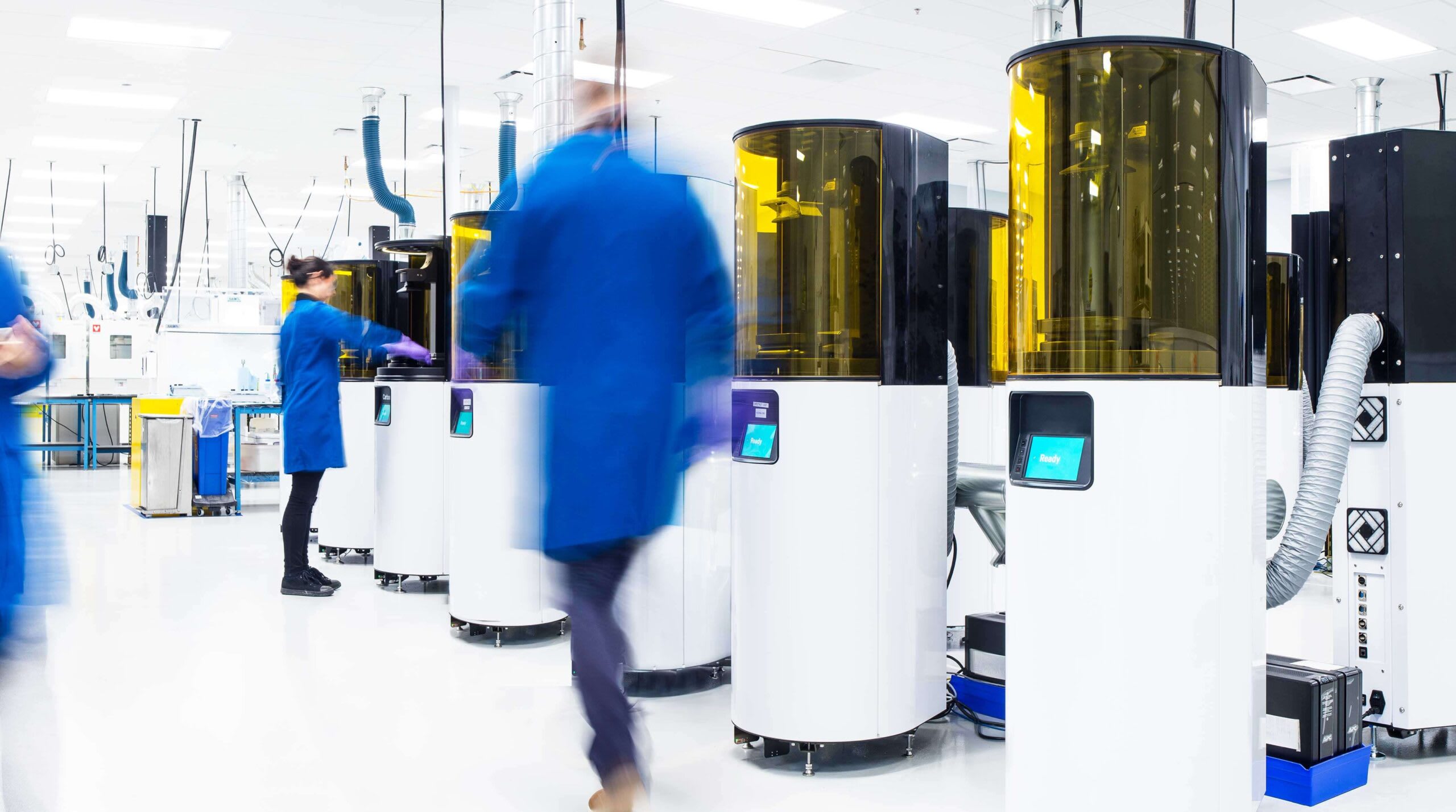
Work with a Carbon Partner
Find a CPN partner that meets your needs and leverage the power of the Carbon platform to design, develop, and produce radically better parts.

Carbon Materials for MedTech Applications
Carbon understands the needs of medical device designers and offers materials that meet functional requirements like strength, comfort, and durability, can be sterilized, and have biocompatible properties.
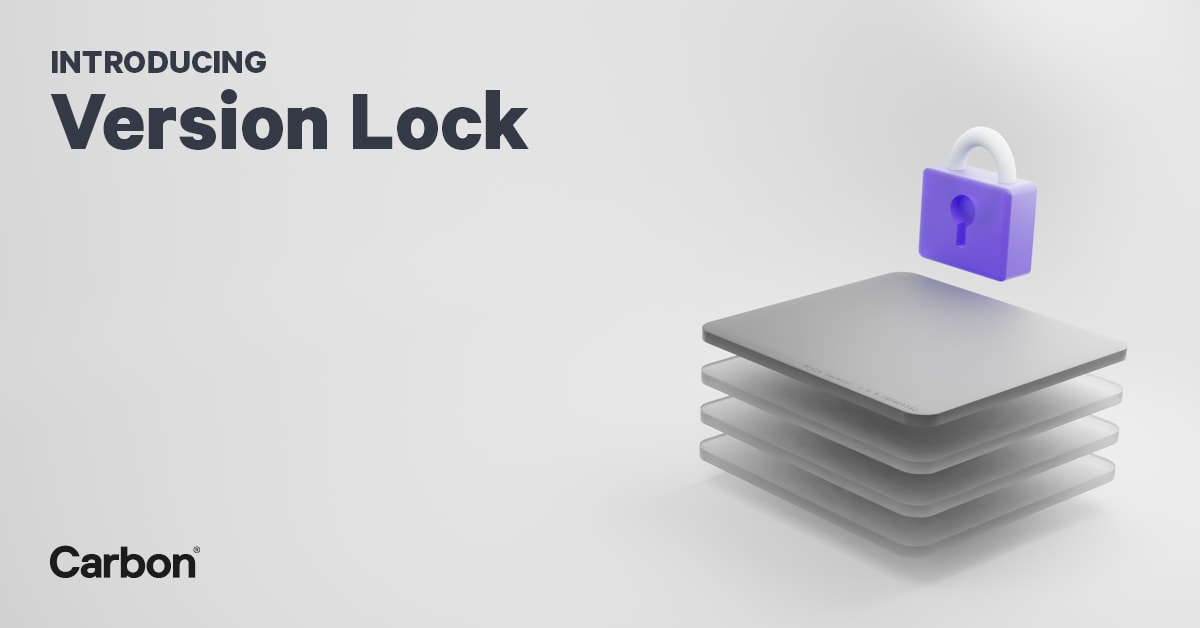
Validated Production for MedTech Applications
While regular over-the-air printer software updates are at the heart of our subscription model, we understand updates can disrupt a validated workflow. With Version Lock, printers can be locked into a current software version to enable MedTech customers to produce using a software version they have validated.
Unlock Design Freedom for MedTech Applications
The Carbon platform helps companies bring new products to market faster by reducing the product development cycle. Print, test, and iterate quickly to consolidate components, manufacture unmoldable geometries, or run low volumes of parts without expensive molds.

Preceptis Medical Hummingbird Tympanostomy Tube System via Resolution Medical
The Hummingbird® device was designed in partnership with leading pediatric ENTs to simplify ear tube procedures and create options for the procedure to be done without general anesthesia. It is FDA 510 (k) cleared for in-office use in children 6 months and older.
After evaluating other manufacturing solutions like low-cost aluminum tooling, Preceptis found the Carbon DLS process with Carbon MPU 100 material via Resolution Medical covered all of their needs thanks to its biocompatible materials, ability to rapidly iterate design, like-molded part quality, and on-demand production capabilities.
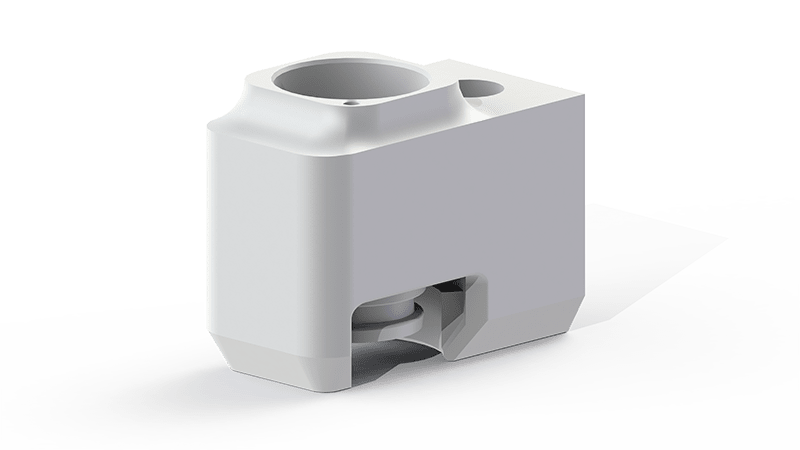
ViscoTec Puredyne Printhead via rpm
ViscoTec is a manufacturer of dosing solutions focused on progressive cavity technology. Its Puredyne® printhead solution, which includes patented single-use cartridges, enables precise dispensing in extrusion-based bioprinting for organ models, cancer research, tissue engineering, personalized medicine, scaffolds, drug development/testing, food, organs-on-a-chip, and cosmetics, among other application areas.
When developing the Puredyne printhead, ViscoTec worked with featured Carbon production partner rpm to utilize the Carbon DLS process and Carbon MPU 100 material for producing the printhead.
Flexible Materials, Even More Flexible Designs
Carbon’s elastomer portfolio combined with lattice designs enables mass customization, multi-zonal support unique to specific pressure maps, and promotes breathability and cleanability for a better patient experience.
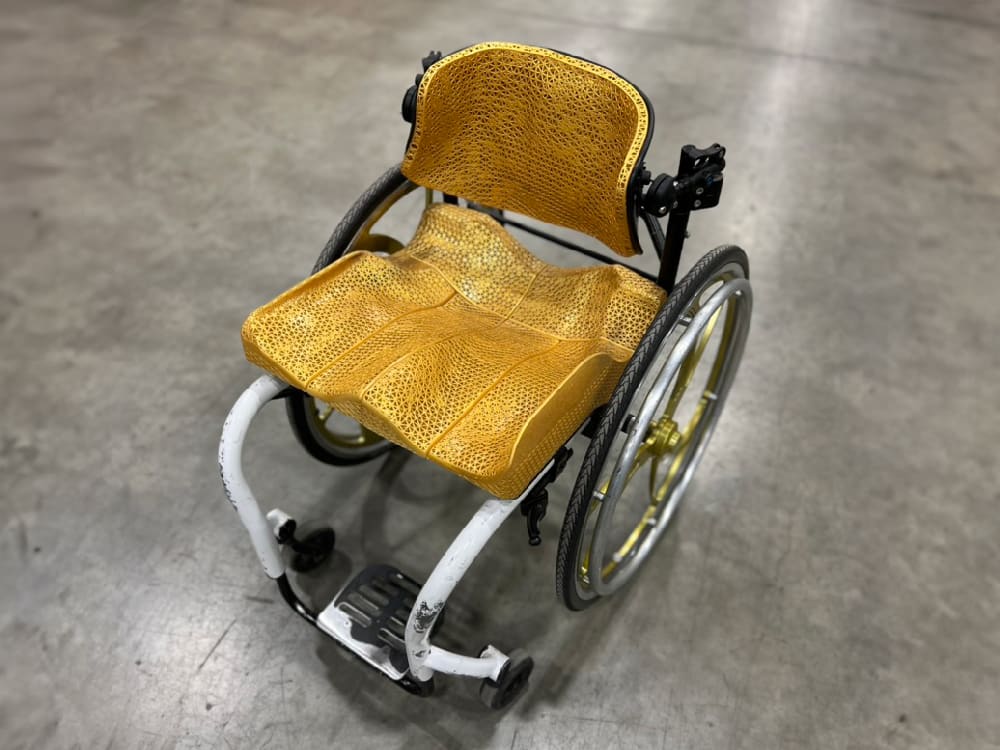
Custom Wheelchair Seating - Tarkka
Tarkka leverages Carbon Design Engine Pro and a variety of Carbon elastomeric materials and colorful coatings to create custom wheelchair seats that are contoured to provide optimal pressure redistribution and maximum comfort for users.

Carbon Design Engine
Carbon Design Engine™ generates multi-zonal lattice designs that can meet key patient needs like pressure relief, custom fit, breathability, comfort and performance. With Carbon Design Engine, designers can precisely control performance characteristics across multiple zones in a product for massive tunability of a single material.