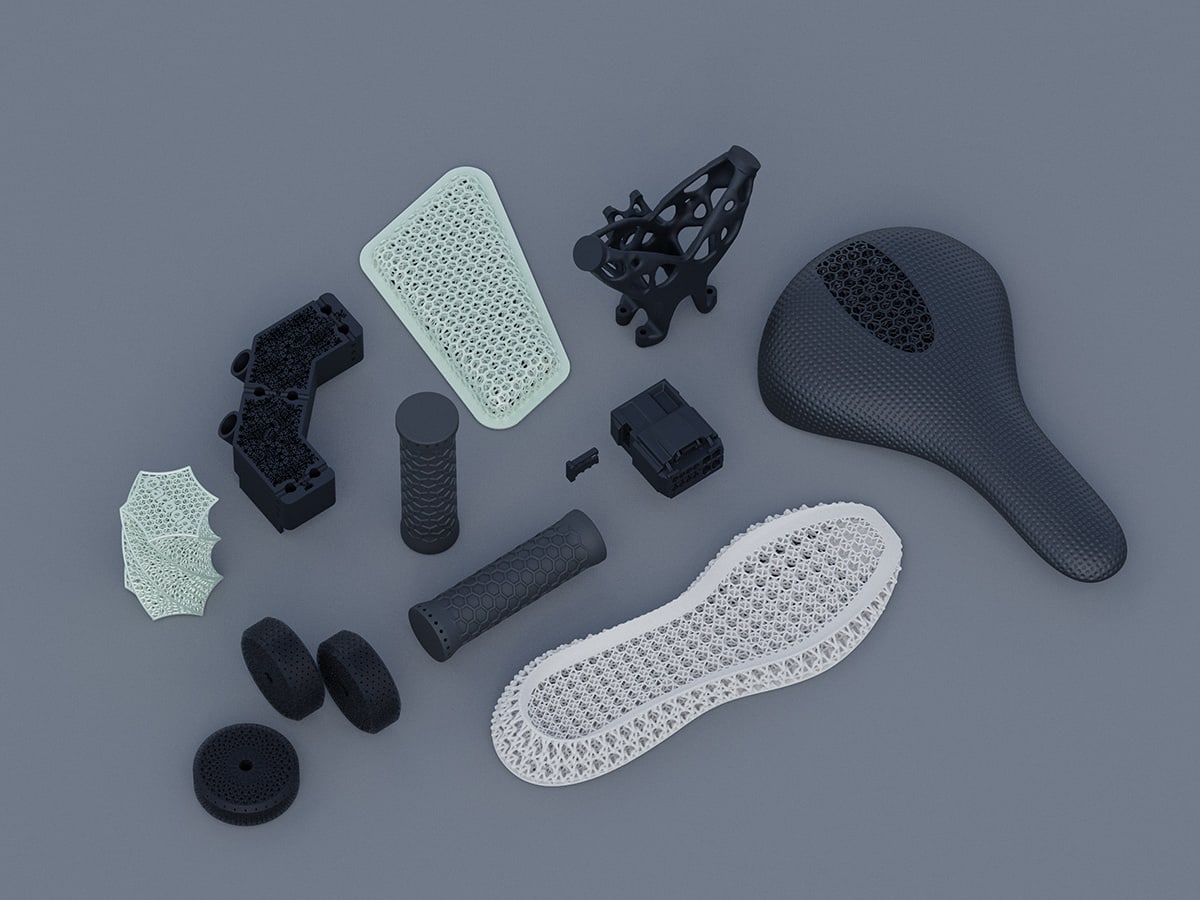
Dual-Cure Materials: Mechanical Properties Set by Heat
Traditional resin-based 3D printing processes produce weak, brittle parts. Carbon overcomes this by embedding a second heat-activated chemistry in our materials. With our dual-cure resins, UV light sets the shape of a part as it prints. The part then undergoes a secondary thermal cure that sets the properties and forms a separate polymer network, which results in robust, engineering-grade mechanical properties comparable to traditional manufacturing plastics, including injection molded parts.
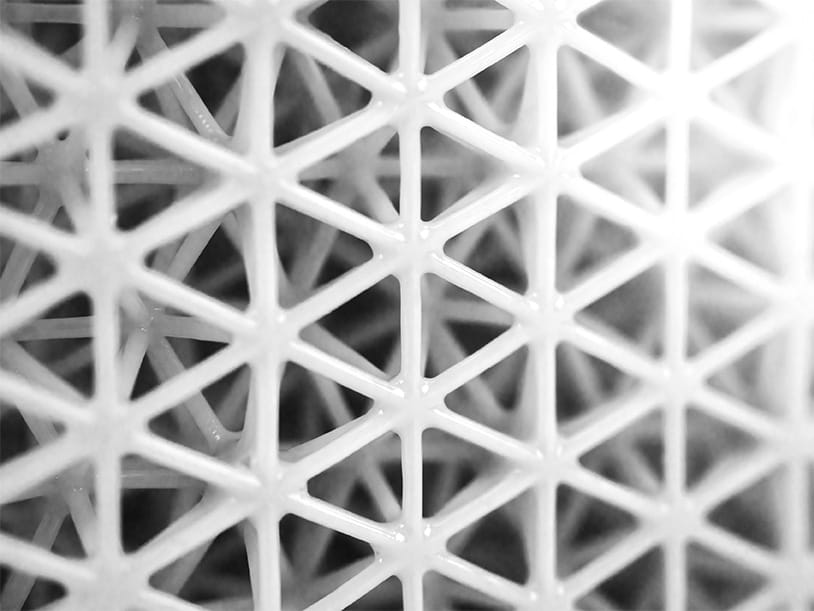
Isotropic Parts with Exceptional Surface Finish
Because of a layer-by-layer process, conventional 3D printed materials often exhibit variable strength and mechanical properties depending on the direction in which they were printed. The Carbon DLS process, on the other hand, produces parts with predictable isotropic mechanical properties. These printed parts are solid on the inside like injection-molded parts and behave consistently in all directions.
The resolution and gentleness of our process—where parts aren’t harshly repositioned with every slice—make it possible to leverage a broad range of materials that meet the surface finish and detail requirements needed for end-use parts.
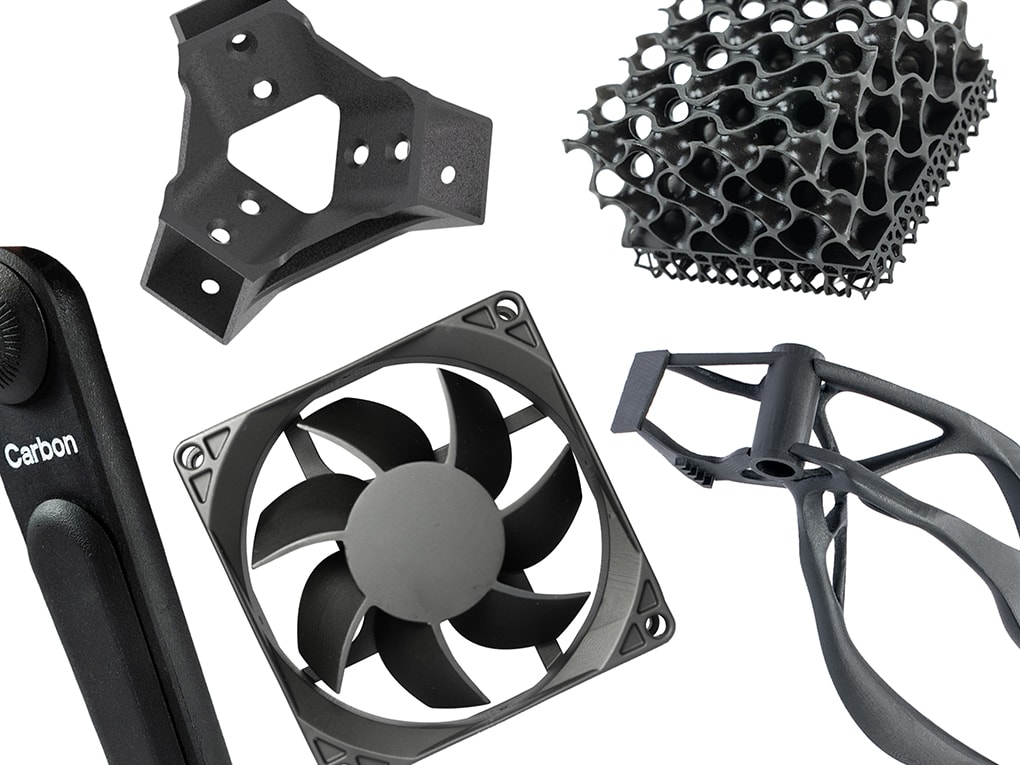
Comparable Carbon Materials for Common Thermoplastics
Carbon offers comparable materials to traditional thermoplastics used in manufacturing. If you’re not familiar with Carbon resins, you may not know where to start in finding a material that will work for your application. The comparison table pairs familiar thermoplastics with Carbon (or Carbon-certified) materials that have equivalent mechanical properties. The best material for your project will depend on which thermoplastic properties are most important in your application.
Learn More about the Carbon DLS Process
The Carbon DLS process is ideal for a wide range of applications, from premium athletic equipment that delivers performance and protection to rugged automotive components that meet stringent engineering requirements.