Paragon Creates Peakyshielder, Comfortable Alternative to the Traditional Face Shield
KEY TAKEAWAYS:
- Paragon designed and produced the Peakyshielder, using Carbon RPU 70 and the Carbon DLS™ process, allowing workers to create a durable yet comfortable face shield with existing headwear
- Using the Carbon DLS™ process, Paragon consolidated the clip’s design from three parts to one, helping reduce assembly costs
- Paragon iterated through five designs within days and sped up the Peakyshielder’s time to market
When the United Kingdom went into lockdown in March 2020, the government quickly provided guidance on protecting against the rapidly spreading SARS-CoV-2 (coronavirus). Face shields were among the most popular forms of front-line protection against virus transmission, especially for healthcare workers. Despite their effectiveness, traditional face shields are often uncomfortable, especially when worn for hours at a time. As a result, many workers outside the healthcare industry don’t wear them.
Duncan Hutchinson, an IT expert and entrepreneur, saw the opportunity to create a non-medical face shield designed to improve comfort and blend in with existing worker uniforms. Hutchinson partnered with Paragon Rapid Technologies Ltd, a UK-based provider of world-class prototyping and manufacturing solutions across a wide range of markets, to begin developing the Peakyshielder, a comfortable and stylish face shield for work and even leisure.
An opportunity to help protect workers
To give the Peakyshielder broad appeal, the design needed to be suitable for prolonged use by production-line workers, customer-facing staff in hospitality and retail, and individuals who cannot wear face masks.
Many workers are unable to use the traditional face shield because they already wear headgear on the job. Production-line workers commonly wear a bump cap—a peaked cap with a reinforced skull cover and a short brim, and many front-line staff in the retail and leisure industries wear a baseball cap or sun visor as a standard part of their uniform. Hutchinson and Paragon knew they needed to design a face shield that could work with various headwear.
Reducing time to market with Carbon
Paragon quickly developed a concept design for the Peakyshielder comprising a pair of clips that can affix a sheet of shaped PET to the brim of a traditional baseball cap, sun visor, or bump cap to create a face shield. The clip prototype was made using Carbon RPU 70, a tough, lightweight, biocompatible 3D printing material with isotropic properties, comparable to ABS. RPU 70’s ability to stand up to the chemicals in cleaners and sanitizers that workers are exposed to was another reason it was ideal for this project.
As alternative forms of face masks became increasingly available, getting the Peakyshielder to market quickly and ensuring cost-efficient short and medium-run production was crucial to ensure the product’s success. To achieve that, Paragon used the Carbon Digital Light Synthesis™ (Carbon DLS™) 3D printing process to remove tooling cycles in the clips’ production process, shortening the development phase and reducing costs.
By using the Carbon DLS™ process, Paragon eliminated the need for tooling, creating a clear advantage over traditional production methods such as injection molding. Paragon possesses the largest Carbon printing capacity in the UK and handled the entire process in-house, from design to production.
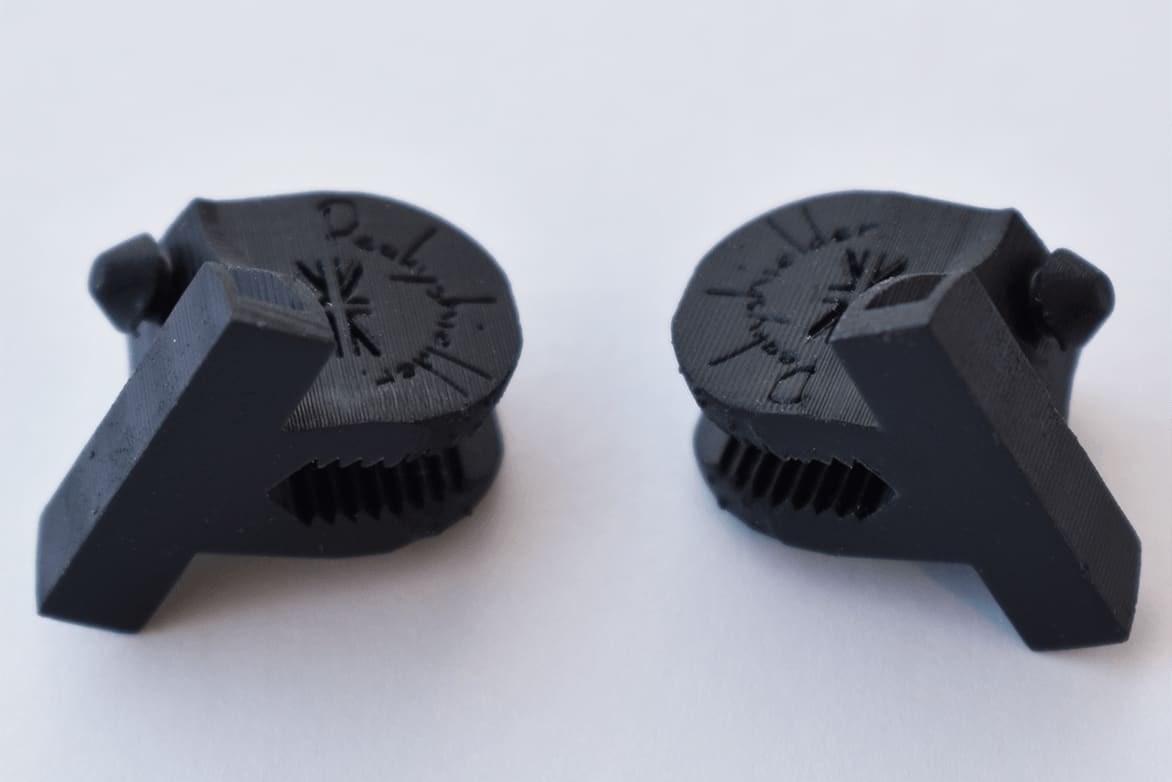
Creating better parts, faster
The initial clip prototype for the Peakyshielder consisted of three components that enable the visor to be swiveled upwards without the wearer having to remove their headwear. However, Paragon realized that there were two significant drawbacks to this concept. First, the clips required assembly, which customers found unappealing and would increase manufacturing costs. Also, the cost of the substantial amount of material needed to create the design would drive up the price of the Peakyshielder, making it uncompetitive against traditional face masks.
The Carbon DLS™ process allows for creating complex designs that traditionally need to be molded in multiple parts and then assembled into one piece. With Carbon, Paragon’s designers simplified the clip design to create a smaller and more robust single unit that increased the maximum possible parts per build and improved production efficiencies.
Paragon was able to go through five design iterations of the Peakyshielder within days using the Carbon DLS™ process. Because bump caps tend to have shorter, thicker peaks than baseball caps, Paragon designed the Peakyshielder clips to be attached to the bump cap’s side panels. To create a second version of the Peakyshielder for baseball caps and visors, Paragon adjusted the PET shield insertion grooves depths and angles on the clips to ensure they attached securely to the brim of baseball caps and sun visors. Once Paragon finalized the two versions of the design, the Peakyshielder clips were produced with the Carbon DLS™ process using Carbon RPU 70.
A face shield solution with many benefits
The UK-produced Peakyshielder provides several advantages over traditional face shields. With its ultra-lightweight and ergonomic construction, the Peakyshielder offers a secure fit with excellent visibility and comfort. The face shield also easily fits over eyewear and can be used along with a standard face mask to provide even greater protection. Last, the Peakyshielder also helps protect the wearer from inadvertent face touching. Workers who have tested the Peakyshielder find it modern and robust and appreciate the easy to clean and reusable clips.
By producing the clip of the Peakyshielder on the Carbon M2 printer, Paragon was able to optimize the production time and throughput by tightly nesting the parts on the build platform. The Carbon DLS™ process, designed for manufacturing, has enabled Paragon to move from prototype to production without incurring additional expense in tooling or iterations.
Interested in learning how the Carbon DLS™ process can speed up your product development? Reach out to Carbon production partner, Paragon Rapid Technologies, here.
3D AS IT'S MEANT TO BE