
Carbon® University Program:
High-Performance Composite Structures Enabled by the Carbon DLS 3D Printing Process
By Alec Redmann, PhD candidate, and Tim A. Osswald, PhD, Professor, Polymer Engineering Center, Department of Mechanical Engineering, University of Wisconsin-Madison
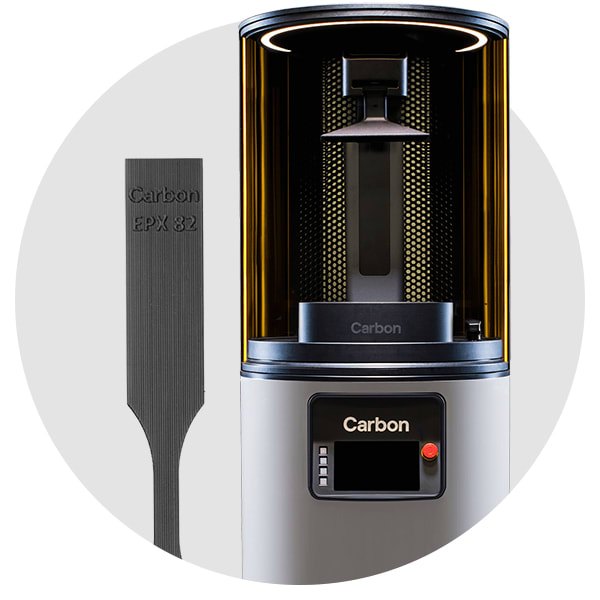
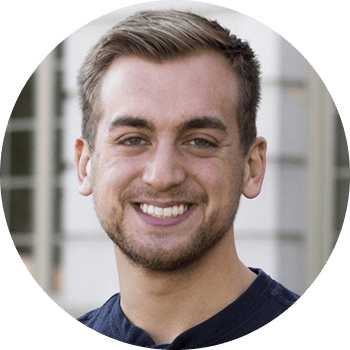
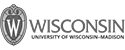
“We instantly realized that this had the power to transform how we think about joining composite structures.”
Alec Redmann
Introduction
Composite materials, specifically fiber reinforced plastics (FRP), are frequently used in aerospace and automotive applications due to their strong mechanical properties and light weight. The designers and engineers in these industries are constantly pushing the boundaries to develop lighter, stronger structures to improve both safety and fuel efficiency.
Research Challenge
FRP parts are notoriously difficult to manufacture. One common manufacturing method involves using sheets of fiber reinforcement embedded in a partially cured resin (for example, carbon fibers in an epoxy matrix). These sheets are cut to the desired shape, placed in a mold, and then thermally cured in an oven to solidify the part. This manufacturing process can only produce basic geometries which then need to be joined together to form the final structure. The two conventional options for joining FRP composites are (1) use mechanical fasteners (metal bolts and screws) or (2) apply adhesive or adhesive tape.
Mechanical fasteners are simple, but add significant weight to the structure and damage the fiber reinforcement, leading to a compromised structure. Adhesive is better in many ways, but for complex geometries you need equally complex fixtures to support the structure before the adhesive can hold it. Imagine how many hands it would take if you tried to apply adhesive and install all the different components of a bicycle frame together at the same time. So we asked ourselves…
How can we more easily manufacture composite structures?
Solution
We continued this conversation on a bus ride to Chicago for an additive manufacturing conference in 2017. We did not realize it at the time, but Carbon was just hours away from announcing the release of its new EPX 82 material, a strong and durable epoxy with functional toughness.
After learning about Carbon’s dual-cure materials and how materials like EPX 82 achieve full, functional mechanical properties through a secondary thermal cure, we instantly realized that this had the power to transform how we think about joining composite structures. Both the composite material and EPX 82 have an intermediate stage that is partially cured––the composite as a pre-impregnated sheet and the EPX 82 as a freshly 3D printed, UV-cured part.
“This approach enabled a completely new type of hybrid composite structure.”
Knowing this, we proposed a new process for manufacturing and joining composites utilizing the Carbon Digital Light Synthesis™ (Carbon DLS™) process and the EPX dual-curing resin:
- The part is 3D printed using the Carbon DLS process and EPX 82 material, resulting in a semi-rigid and partially cured part.
- In this intermediate stage, the EPX 82 part is integrated with a compatible pre-impregnated fiber reinforcement.
- The assembly is then heated in an oven to activate the thermal-curing reaction and co-cure the two materials, forming a permanent, void-free bond.
This approach of incorporating an EPX 82-printed core with fiber-reinforced face sheets not only provided a better technique for joining, but also enabled a completely new type of hybrid composite structure.
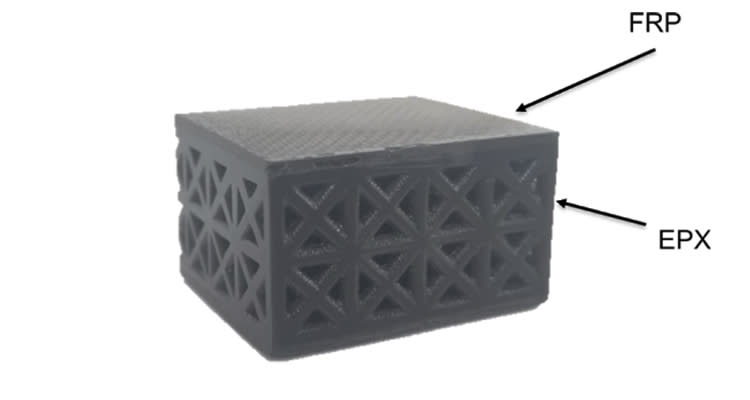
Additionally, the design flexibility of the Carbon DLS process allowed for highly optimized core structure designs. A latticed core structure can be designed as any shape and have variable thickness and density. This has the ability to eliminate the traditional steps associated with preparing honeycomb core structures for composite sandwich panels, such as cutting the core to size, molding and machining to shape, adjusting the density where added strength is needed, and applying potting compounds to specific regions. The ability to print optimized, ready-to-use core structures could streamline manufacturing processes for sandwich structures in the future.
Testing
To test the idea, we first manufactured single-lap shear samples with composite plates bonded together by EPX. The samples were pulled in tension, and the strength of the bond was compared to a traditional epoxy adhesive (3M™ Scotch-Weld™ DP190) and standard lap shear joint with no secondary adhesive (EP4030). The results were promising, showing the EPX provided a high bonding strength suitable for structural loads.
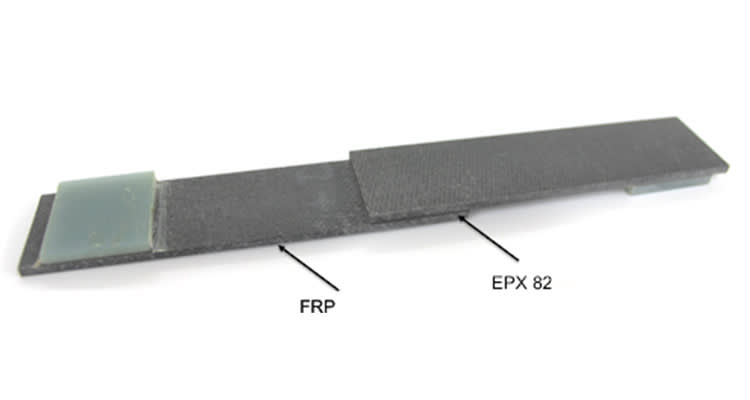
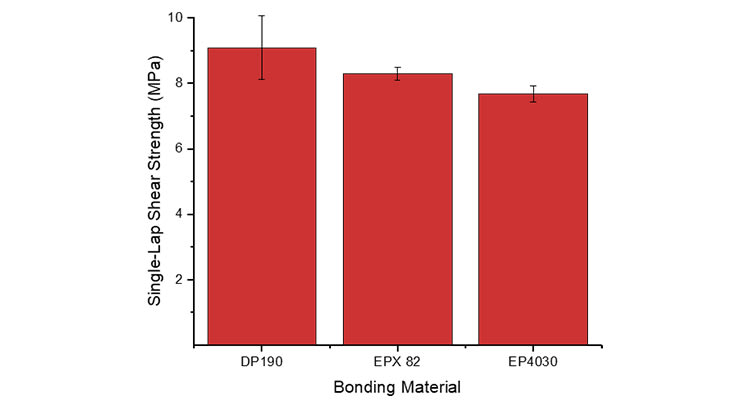
“Combining these two technologies enables the economic mass production of light-weight composite truss structures.”
Application Areas
Discussions with our colleagues working with aerospace structures prompted the first demonstrated application for EPX 82 as an adhesive material. There are many instances when composites must be used in sharp angles, but due to the limitations in how much the material can bend, a gap is formed in the structure. This gap is known as the “deltoid” and must be filled in some way to properly transmit the in-flight loads. The spar/wingskin structure in a wing is one example of a structure with these T-joints. There are different ways of filling the deltoid region, but none are as simple as 3D printing the exact shape you need. Changing geometry to account for a different radius or angle is as simple as changing the CAD file and printing a new part. Major benefits in manufacturing time and reproducibility were observed.
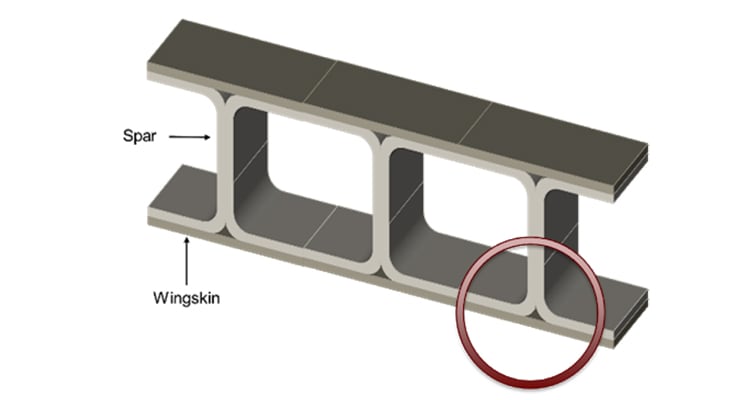
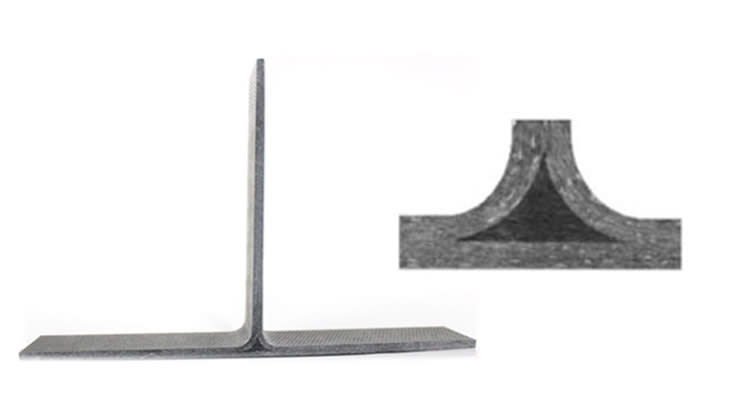
Another application is currently being developed in partnership with the wbk Institute of Production Science at the Karlsruhe Institute of Technology. Hollow profiles made of fiber-reinforced composites are ideally suited for the production of highly rigid, lightweight truss structures. Due to their excellent mechanical properties and ability to be economically mass produced, these structures follow the current trend toward resource-efficient construction. However, the same major challenges still exist in the fabrication and joining process of these composite structures.
An innovative winding process has been developed for the production of lightweight structures by autonomously joining these composite profiles. The robotic winding device allows a high degree of flexibility and design variety in the winding patterns. The open ring construction enables collision-free production of closed-frame structures, which is not possible with any other conventional winding processes. We can use the EPX joining elements to hold the profiles in place during winding, allowing more flexibility in the process. Combining these two technologies enables the economic mass production of light-weight composite truss structures and promotes the adoption of composite materials in a range of applications for which they were previously cost-prohibitive.
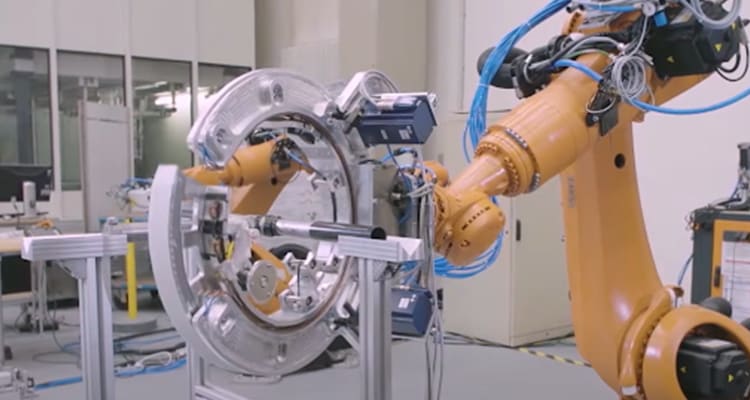
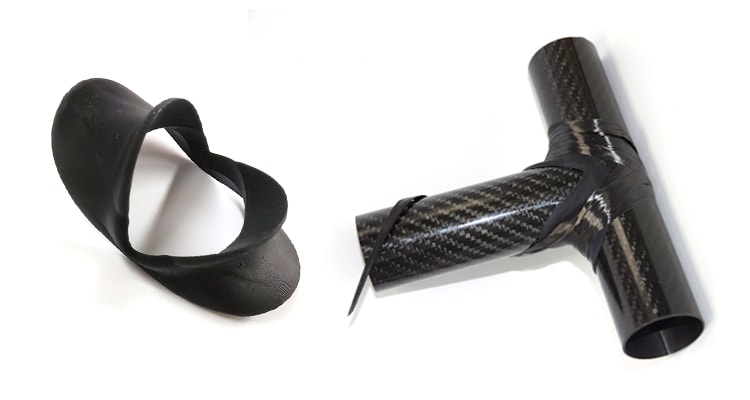
Conclusion
This research bonding composite structures with Carbon DLS dual-curing technology is still in its infancy, and we are sure there are countless more applications yet to be discovered. We look forward to working with Carbon and our industry partners to find ways we can continue to improve the composite manufacturing process.
3D as It’s Meant to Be
To learn more about composite structure research at Wisconsin and how Dr. Osswald’s group is leveraging the Carbon DLS process, click here.
Interested in using the Carbon DLS process for your research efforts? Reach out to us at sales@carbon3d.com to learn more about the Carbon® University Program.