The Carbon DLS Process
Digital Light Projection: UV Light Shapes the Part
The Digital Light Synthesis process is driven by Carbon’s groundbreaking Continuous Liquid Interface Production, or CLIP. CLIP is a photochemical process that cures liquid plastic resin into solid parts using ultraviolet light. It works by projecting light through an oxygen-permeable window into a reservoir of UV-curable resin. As a sequence of UV images is projected, the part solidifies and the build platform rises.
Oxygen-Permeable Optics: Fast Printing via the “Dead Zone”
The heart of the CLIP process is the “dead zone”—a thin, liquid interface of uncured resin between the window and the printing part. Light passes through the dead zone, curing the resin above it to form a solid part without curing the part onto the window. Resin flows beneath the curing part as the print progresses, maintaining the “continuous liquid interface” that powers CLIP and avoiding the slow and forceful peeling process that is inherent to many other resin-based printers.
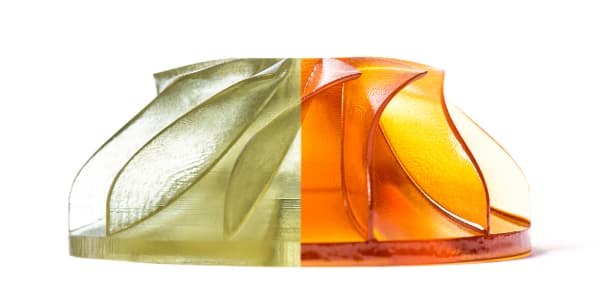
Right: Cured Young's Modulus (3800 - 4000 MPa)
Dual-Cure Materials: Mechanical Properties Set by Heat
Traditional resin-based 3D printing processes produce weak, brittle parts. Carbon overcomes this by embedding a second heat-activated programmable chemistry in our materials. Once a part is printed on a Carbon printer, it’s baked in an oven. Heat sets off a secondary chemical reaction that causes the materials to adapt and strengthen, taking on exceptionally strong characteristics. This produces high-resolution parts with engineering-grade mechanical properties.
The Results? Isotropic Parts with Exceptional Surface Finish
3D printed parts are notoriously inconsistent. Because of a layer-by-layer process, conventional 3D printed materials often exhibit variable strength and mechanical properties depending on the direction in which they were printed.
The Carbon DLS process, on the other hand, produces parts with predictable isotropic mechanical properties. These printed parts are solid on the inside like injection-molded parts and behave consistently in all directions. The resolution and gentleness of our process—where parts aren’t harshly repositioned with every slice—make it possible to leverage a broad range of materials that meet the surface finish and detail requirements needed for end-use parts.
The Carbon Isotropic Difference
Stage 01: Print
The isotropic difference of parts printed on the Carbon platform is due in part to the dead zone. In this small region, a thin layer of oxygen prohibits curing closest to the window with its effect falling off to zero at ~20 µm from the surface of the window.
Liquid resin begins to intersect and cure along the z-axis as light escapes the oxygen layer of the dead zone.
Stage 02: Bake
Each stage in the process contributes to the mechanical integrity of every printed part.
The isotropy of each printed part is reinforced with a thermal curing stage. Here, a secondary reaction creates a molecular weaving, adding strength in all directions.
Fully Dense Parts with End-Use Quality
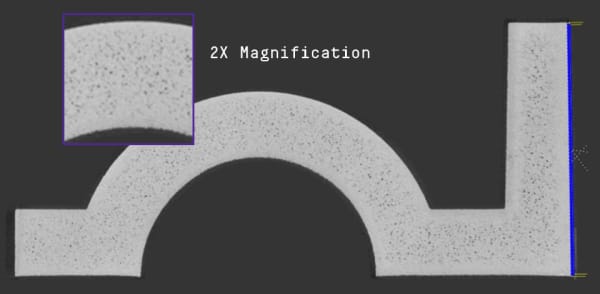
Powder-Bed Fusion
Carbon DLS
Unlike powder-bed fusion 3D printing technologies, Carbon technology produces fully dense parts.
Why the Carbon DLS Process?
Accelerate Every Step of Product Development
Rapid Design Iterations
Test dozens of designs in the time it used to take to try one.
Functional and Rapid Prototyping
Don’t settle for fragile prototypes. Bring your designs to life with the industry’s best materials, then start testing and iterating immediately.
Scale to Production
Seamlessly transition into production, while still having the ability to revise your designs immediately and without retooling. Scaling has already been done by leading brands like adidas, Specialized, and fizik.
Find the Perfect Design for Your Application, Not the Mold
Undercuts and Undrafted Walls
Moldability constraints don’t apply here. Enjoy the freedom of designing with undercuts and perfectly straight walls without sacrificing manufacturability.
Performance-oriented Lattices
Lattices allow you to specify your required characteristics at every millimeter. Determine your product’s ideal mechanical response and leverage Carbon Design Engine™ software to generate the right lattice for it.
Consolidated Parts
A single printed part frequently offers better overall mechanical performance than an assembled part. Streamline production with reduced SKUs and less labor by consolidating assemblies.
Discover New Aesthetics
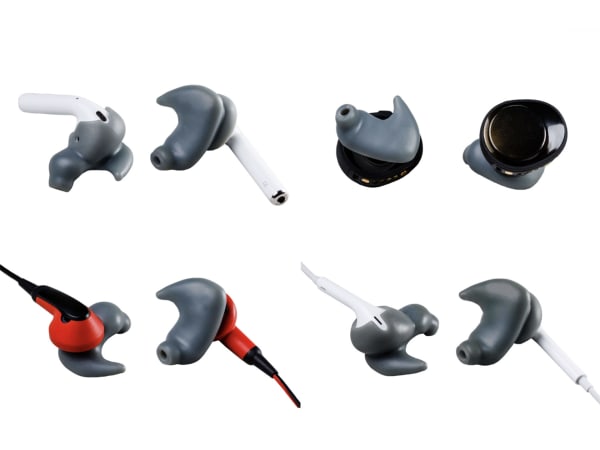
Customization
With no tooling costs, you’re free to make every unit unique. Offer personalized designs, or build entire products around individuals.
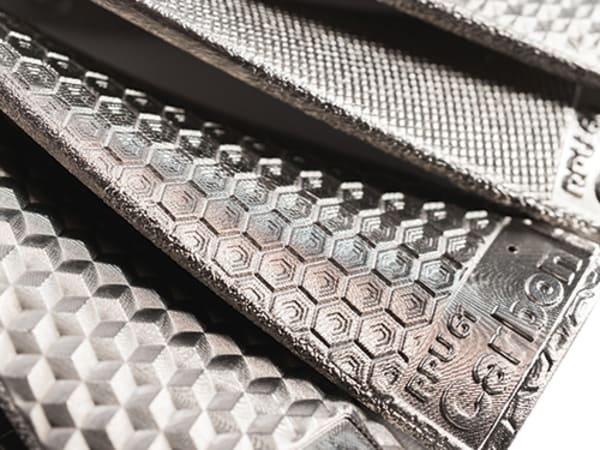
Surface Design and Textures
Enhance your parts by applying textures to complex curved surfaces like grips and enclosures with Carbon design software.
Perfecting Product Design with the Carbon DLS Process
3D printing sends modern design soaring, giving designers and engineers the freedom to bring their most inspired ideas to life without the constraints of molding or machining.
Learn about how the Carbon DLS process unlocks a new world of design.